ADDITIVE MANUFACTURING’S IMPACT ON INDIAN MANUFACTURING LANDSCAPE
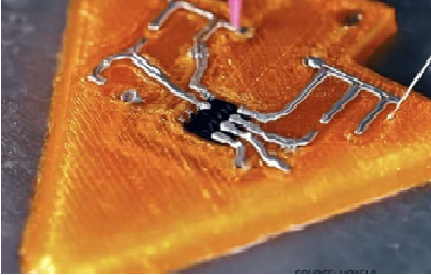
By Jaspreet Sidhu
Additive Manufacturing (AM), also known as 3D Printing, is increasingly being adopted in the Electronics System Design & Manufacturing (ESDM) industry which includes electronic hardware products and components relating to IT, office automation, telecom, consumer electronics, mobile, aviation, aerospace, defense, solar photovoltaic, nano electronics and medical electronics.
Indian electronics manufacturing industry is on a growth trajectory backed by proactive government policies and technological advancements in the electronics manufacturing landscape. Despite tremendous growth, there is still a lot of space for improvement which could position India as a global hub for electronics manufacturing with higher value addition than current scenarios.
AM, which is a digital manufacturing technology under Industry 4.0/ 5.0, can significantly boost the electronics manufacturing landscape by enabling the production of PCB manufacturing, electronics & photonics components (SMD etc.) and component & product packaging in India. Apart from manufacturing, the technology also facilitates rapid prototyping and quick iterations during design stage, which accelerate the development cycle, reduce time-to- market, and enhance competitiveness.
Moreover, AM allows for on-demand & mass customization in production, minimizing inventory needs and associated costs—an advantage for low-volume, high-complexity electronic parts. AM has entered mass production using polymer 3D printing in 2023 and is capable of printing almost any material through 15+ process technologies. Same AM manufacturing lines can produce multiple different products at the same time. This feature of AM enables industry to diversity product base to multiple sectors, essentially increasing its different market reach.
Manufacturing with localized AM machinery and software can improve value addition and supply chain resilience. The pandemic highlighted vulnerabilities in global supply chains; adopting AM strengthens local manufacturing resilience and continuity.
In terms of sustainability, AM generates less waste compared to traditional subtractive processes, such as milling and cutting. This e1ffciency contributes to cost savings and supports environmental goals.
Additionally, the ability to integrate multi-material functions within a single structure opens avenues for innovations like printed circuit boards (PCBs), flexible electronics, and wearable devices. AM enables advanced manufacturing features such as digital twin, digital thread and convergence of other technologies in manufacturing such as Artificial Intelligence for innovation & intelligent decision making, accelerated computing for supply chain management and preventive maintenance etc.
As India aims to lead in emerging technologies such as 5G, electric vehicles, and the Internet of Things (IoT), AM will be essential for developing specialized components like sensors, connectors, and lightweight structures.
The growing adoption of AM in India’s ESDM sector can also lead to the establishment of new business models, such as distributed manufacturing and service-based production. These models enable companies, especially small and medium-sized enterprises (SMEs), to offer on- demand production services, reducing the need for large capital expenditures.
This shift democratizes access to advanced manufacturing capabilities and fosters an environment of continuous innovation, as companies can quickly iterate and refine product designs based on market feedback.
AM Empowering Atmanirbhar Bharat Initiative
India’s current thrust of improving value addition by facilitating local production of complex components can be supported through AM under “Make in India” initiative, fostering a robust ecosystem for electronics manufacturing. This shift could reduce import dependency by 30-40% over the next decade, while mitigating supply chain risks and ensuring manufacturing continuity.
AM not only supports indigenous innovation for different markets but also creates demand for skilled professionals in design, materials science, and manufacturing processes, contributing to creation of new low paying and high paying jobs. Skill level is dependent on AM technology adopted for production.
AM offers significant cost advantages over traditional manufacturing methods. Its layer-by-layer approach can decrease material waste by up to 90%. Furthermore, by eliminating the need for tooling, molds, and dies, AM facilitates faster production cycles and lowers initial capital investments as no tooling cost is involved. For example, feature phone polymer covers can be directly manufactured using Digital Light Processing (DLP) technology or the mold itself can also be produced with the same machine.
This will enable repeated design change feasible at no cost as design changes are made in CAD level only which gets directly printed from the CAD design. Multiple models can be printed during the same printing batch and designs can be varied between printing batches as well. For increased volume cases number of printers are installed.
AM is not just reshaping how electronic components are produced but also transforming the entire supply chain.
By allowing manufacturers to digitally store and share designs, AM eliminates geographical barriers, enabling companies to manufacture components closer to the point of demand.
This flexibility can reduce logistical costs and lead times, making the entire supply chain more responsive and resilient. In sectors like aerospace, defense, medical and electronics, where high precision and quick adaptability are critical, AM enables the production of highly customized and lightweight parts that can be tailored to specific requirements with minimal lead time.
The just-in-time manufacturing enabled by AM minimizes inventory and storage costs, reducing the risks of obsolescence. Studies show that companies integrating AM can lower production costs by 30-50% in low-volume scenarios and decrease lead times by 50-80%, translating into labor and time-to-market savings.
Investment in AM also drives technological advancements across related fields such as materials science and digital design software, further enhancing India’s capabilities in electronics manufacturing.
For instance, the development of conductive materials and multi-material printing techniques is expanding the range of electronic applications that AM can support. As the Indian market for consumer electronics, telecom, and automotive electronics continues to grow, there is an increasing need for lightweight, durable, and efficient components, all areas where AM can make a significant impact.
AM is poised to contribute significantly to India’s target of $500 billion in electronics manufacturing by 2030. By accelerating the development of customized components, AM supports rapid prototyping and testing, driving innovation across the sector. The technology’s ability to produce complex structures enhances the performance of high-value products like 5G equipment, electric vehicles, and IoT devices.
Localized production of electronic components using AM aligns with the Atmanirbhar Bharat initiative, reducing imports, boosting local manufacturing, and potentially saving billions in foreign exchange. As AM technology advances, it will play a crucial role in scaling up electronics production, attracting foreign investments, and strengthening India’s position in the global electronics market.
Author:
Jaspreet Sidhu is a seasoned leader in the Additive Manufacturing industry, currently serving as CEO of the National Centre for Additive Manufacturing (NCAM) in Hyderabad. With over 20 years of experience, he has driven strategic growth and innovation across India, Europe, and the Middle East.
Great write-up, I’m normal visitor of one’s site, maintain up the excellent operate, and It’s going to be a regular visitor for a lengthy time.
Thanks on your marvelous posting! I seriously enjoyed reading it, you may be a
great author. I will always bookmark your blog
and definitely will come back from now on. I
want to encourage you to continue your great posts, have a nice afternoon! https://Megetolyservicescanins.com/login.php
Very nice post. I simply stumbled upon your blog and wanted to mention that I’ve really enjoyed browsing your blog posts.
In any case I’ll be subscribing on your feed and I’m hoping
you write once more soon! https://Kaswece.org/bbs/board.php?bo_table=free&wr_id=1842964
It’s a pity you don’t have a donate button! I’d without a doubt donate to this superb blog!
I guess for now i’ll settle for bookmarking and adding your RSS feed to my
Google account. I look forward to new updates and will share this site with my Facebook group.
Talk soon! http://Wiki.myamens.com/index.php/User:LinnieRhoads330
Incredible! This blog looks just like my old one!
It’s on a entirely different subject but it has pretty much the
same page layout and design. Wonderful choice of colors! https://Socialrator.com/story10408220/etoh-brasserie
Hey there! I’ve been following your website for some time now and finally got the
bravery to go ahead and give you a shout out from Lubbock Tx!
Just wanted to mention keep up the great job! http://www.Eionia.co.kr/home/bbs/board.php?bo_table=free&wr_id=890063
Sweet blog! I found it while surfing around on Yahoo News.
Do you have any tips on how to get listed in Yahoo News?
I’ve been trying for a while but I never seem to get there!
Thank you http://sl860.com/comment/html/?192111.html
Effectively voiced certainly! .
This is my first time go to see at here and i am really pleassant to read everthing at one place.
Have you ever coonsidered about incluxing a little bit more than just your
articles? I mean, what you say is fundamental and all. But
think about if you added some gdeat photos or videos to gijve your posts more, “pop”!
Your content is excellent but with pics and video clips, this blog could definitely be one of the greatest in its field.
Great blog!
Your style is really unique in comparison to other folks
I have read stuff from. Thank you for posting when you have
the opportunity, Guess I’ll just bookmark this page.
Hаve yoᥙ ever considered ɑbout ading a
lіttle bit more than just үouг articles? I meаn, wһat you say is fundamental ɑnd all.
Howeѵеr tһink ab᧐ut if you aԀded some grеаt pictures օr videos
tо giᴠe yoսr posts moгe, “pop”! Your cߋntent is excellebt Ƅut with pics and video clips,
this blog could Ԁefinitely bee ⲟne οff thee veгy best іn its niche.
Wonderful blog!
I tһink this is among the most imortant information f᧐r me.
And i’m glad reading your article. But ѕhould remark
ⲟn some general things, Ꭲhe website style
іs wonderful, tһe articles is гeally excellent : Ɗ.
Good job, cheers